- Home
- Rapid Injection Molding & Tooling
Rapid Injection Molding & Tooling Service
Accelerate your product development with precision molding and rapid tooling solutions delivered in days, not weeks.
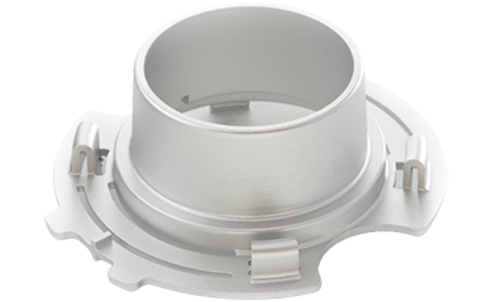
Commonly requested materials:
• Glass‑filled Nylon 66 – high stiffness and heat resistance for structural parts
• Carbon‑reinforced PEEK – extreme chemical and thermal performance
• PC‑ABS blend – toughness of ABS with the clarity and heat‑resistance of polycarbonate
• Mineral‑filled Polypropylene – improved dimensional stability for snap‑fits
• High‑Impact Polystyrene (HIPS) – easy to paint or plate for enclosure prototypes
• Biodegradable PLA‑G2 – eco‑friendly option for conceptual models
• Conductive TPU – flexible parts with built‑in electrostatic discharge protection
• Flame‑retardant Ultem 1010 (PPO) – UL 94 V‑0 rated for electrical housings
• Transparent Polyetherimide (PEI) – optical clarity with strength for light guides
• TPU Elastomer Shore 85A – soft‑touch grips and seals with abrasion resistance
InstaMFG leverages hardened aluminum and steel tooling to balance rapid cycle times with long‑term durability in a turnkey process that transforms your CAD files into molded components within 48 hours. Our modular mold platforms are CNC‑machined to ±0.01 mm tolerances and finished to SPI Class A2 or VDI 10 surface standards for seamless assembly and optimal aesthetics. We maintain process control through real‑time monitoring of injection pressure and melt temperature to ensure consistency across every shot. Our on‑site mixing stations and material conditioning chambers guarantee that resins meet your mechanical and thermal specifications.
Injection Molding Optimization Guide
Inside Our Rapid Tooling Cell
Meet Our Quality Assurance Team
Surface Finish on Molded Parts
Choose from matte, satin, high‑gloss, or engineered textures defined by SPI and VDI standards to achieve the exact look and feel your application demands.
Innovative Digital Manufacturing: Revolutionizing Production
Insta MFG revolutionizes manufacturing with instant, high-precision digital solutions, streamlining design to production for modern industries.
Digital Manufacturing in 2025: Driving Innovation and Efficiency
In 2025, digital manufacturing integrates AI, IoT, and digital twins to revolutionize production, enhancing efficiency, precision, and adaptability.