- Home
- Sheet Metal Prototyping Service
Sheet Metal Prototyping Service
Accelerate your product development with InstaMFG’s sheet metal prototyping services. Our rapid fabrication process transforms your CAD designs into functional metal prototypes, enabling swift iterations and reducing time-to-market.
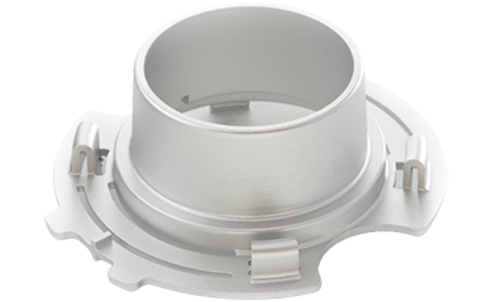
Materials & Finishes
We offer a diverse selection of metals and finishing options to meet your project’s specific requirements:
Metals: Aluminum, Stainless Steel, Cold-Rolled Steel, Copper, Brass
Finishes: Powder Coating, Anodizing, Brushed, Polished, Bead Blasting
Our materials are sourced to ensure durability and performance, while our finishing processes enhance both aesthetics and corrosion resistance.
Prototyping Process Overview:
Our sheet metal prototyping process encompasses:
Design Review: Collaborative evaluation of your CAD files for feasibility.
Material Selection: Choosing the appropriate metal and thickness.
Cutting & Forming: Precision laser cutting followed by bending and forming.
Assembly: Welding or fastening components as needed.
Finishing: Applying the selected surface treatment.
Quality Inspection: Ensuring the prototype meets all specifications.
This streamlined workflow ensures high-quality prototypes delivered promptly.
“Effective sheet metal prototyping begins with thoughtful design—ensuring uniform material thickness, appropriate bend radii, and strategic placement of features relative to bends. These considerations not only enhance manufacturability but also ensure functional integrity and cost-efficiency.”
Applications
Quality Assurance
Sheet Metal Prototyping Best Practices
Designing for sheet metal prototyping involves several key considerations to ensure manufacturability, functionality, and cost-effectiveness. One fundamental aspect is selecting the appropriate material thickness. This choice impacts the part's strength, weight, and the feasibility of forming processes. It's essential to maintain uniform thickness throughout the part to prevent issues during fabrication and ensure consistent quality . Another critical factor is the design of bends and flanges. Incorporating standard bend radii and reliefs helps mitigate the springback effect and reduces the risk of metal tearing. Utilizing standard die sets, such as 0.80 mm (0.030″) tools for internal corners, can be advantageous. Alternatively, consulting with your fabricator about the available tools is essential to ensure compatibility . Additionally, accounting for features like holes and slots is crucial. It's recommended to place holes and slots at least 3 mm away from bend lines to prevent deformation during bending. This distance helps maintain the integrity of the part and ensures accurate hole placement . By adhering to these best practices, you can optimize your sheet metal designs for prototyping, leading to more efficient production processes and higher-quality prototypes.
Innovative Digital Manufacturing: Revolutionizing Production
Insta MFG revolutionizes manufacturing with instant, high-precision digital solutions, streamlining design to production for modern industries.
Digital Manufacturing in 2025: Driving Innovation and Efficiency
In 2025, digital manufacturing integrates AI, IoT, and digital twins to revolutionize production, enhancing efficiency, precision, and adaptability.