- Home
- 4 Axis CNC machining
4 Axis CNC machining
4 Axis CNC machining integrates a rotary axis—typically a turning fixture—perpendicular to the standard X, Y, and Z axes. This additional B-axis rotation allows the cutting tool to approach the workpiece from four distinct directions without manual re-clamping. The outcome is fewer setups, streamlined workflows, and the ability to produce intricate features such as helical shapes, undercuts, and deep cavities
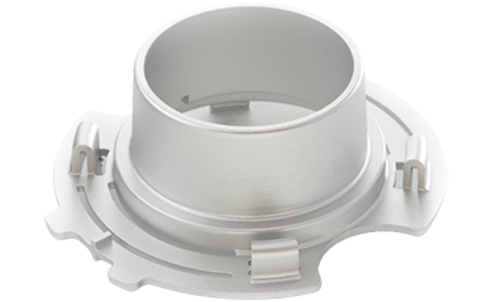
Key Benefits:
We offer high-quality 4-Axis CNC machining with the following advantages:
Reduced Setup Time & Costs
Fewer part re-clamps mean less downtime and lower labor expenses.Higher Precision & Accuracy
Consistent tool-to-workpiece angles achieve tighter tolerances (±0.005 mm or better).Superior Surface Finish
Continuous rotary cutting avoids step marks, delivering smoother contours.Complex Geometry Capability
Machine hooked, angled, or spiral features in one go—ideal for turbine blades and medical implants.Expanded Material Range
From aluminum and stainless steel to titanium and high-performance plastics.
Applications:
4 Axis CNC machining powers critical industries where complexity and precision converge:
Aerospace: Turbine blades, structural brackets, and housings.
Automotive: Custom camshafts, manifolds, and prototype parts.
Medical: Surgical instruments, orthopedic implants, and dental prosthetics.
Mold & Die: Intricate mold cavities and undercuts without multiple fixtures.
Design & Programming
Setup & Fixturing
Rough Machining
Finish Machining
Design & Programming
CNC engineers prepare 3D CAD models and CAM toolpaths, defining rotary axis motions for seamless 4-axis operations.
Setup & Fixturing
Parts are mounted on a rotary table or 4th-axis fixture; zero-points are established for all axes.
Rough Machining
High-feed strategies remove bulk material quickly while rotating the part to different angles.
Finish Machining
CMM and surface-profilometer checks verify tolerances and finish against specifications.

Functional Prototyping & Validation with 4-Axis CNC Machining
Why Choose InstaMFG’s 4 Axis CNC Machining
State-of-the-Art Equipment: We employ the latest Haas and DMG MORI 4-axis centers. Expert CAM Programming: Our team optimizes toolpaths for speed and precision. Tight Tolerances: Certified quality control to ±0.005 mm. Fast Turnaround: Rapid prototyping and high-volume production under one roof. Ready to transform complex designs into reality? Request a Quote │ View Case Studies
Innovative Digital Manufacturing: Revolutionizing Production
Insta MFG revolutionizes manufacturing with instant, high-precision digital solutions, streamlining design to production for modern industries.
Digital Manufacturing in 2025: Driving Innovation and Efficiency
In 2025, digital manufacturing integrates AI, IoT, and digital twins to revolutionize production, enhancing efficiency, precision, and adaptability.